Components integration as the path toward decarbonization in the cooling sector
By Andre Paz Rosa, Commercial Appliances R&D and Product Strategy Senior Director for Nidec Global Appliance, Embraco’s brand owner …
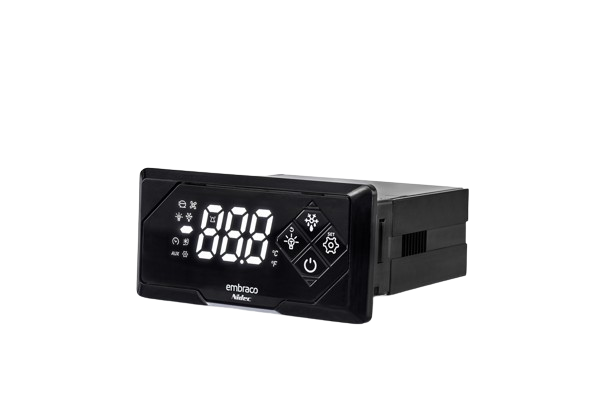
By Andre Paz Rosa, Commercial Appliances R&D and Product Strategy Senior Director for Nidec Global Appliance, Embraco’s brand owner
The world has been facing a monumental challenge: global warming and the resulting climate change. According to the Copernicus Climate Change Service, the European Union’s Earth Observation Programme, January 2024 marked the eighth month in a row with global temperatures rising by 1.3-1.7 degrees Celsius above the average. In response to this urgency, decarbonization has become a global priority.
The cooling industry is essential to the preservation of food, beverages, medicine, vaccines, lab samples and the list of its importance to mankind goes on and on. It means quality of life, comfort, and health. But, on the other hand, it is responsible for approximately 10% of global CO2 emissions, according to some estimates researched by Birmingham University, in a study about clean cooling.
The study also says that “around 20%-25% of CO2 equivalent emissions from the cooling sector are produced by leaks of hydrofluorocarbon refrigerant gases (‘F-gases’)”. The other 75% of the cooling sector’s emissions, still according to the same study, come from energy consumption. Another research institute, the IIR (International Institute for Refrigeration), by its turn, says that the cooling sector (including refrigeration and air conditioning) consumes about 17% of the overall electricity used worldwide.
This reality makes it crucial to reduce energy consumption on the refrigeration industry’s path toward decarbonization, as energy generation is still predominantly based on highly polluting sources such as natural gas, coal, and other petroleum derivatives. According to the United States Environmental Protection Agency, in 2022, the electric power sector was responsible for 34% of the global greenhouse gas emissions.
Energy efficiency is the fastest and most affordable way to decarbonize our economy and ensure reliable and sustainable energy for everyone on the planet. According to an IEA (International Energy Agency) report, it is the path that accounts for 44% of the emissions reductions in IEA’s Sustainable Development Scenario, in relation to other actions, such as renewable energy, nuclear energy, etc.
In the commercial refrigeration segment, to address this challenge, it is essential to adopt technologies that allow us to consume less energy without compromising cooling performance since the market demands sustainability with efficiency, flexibility, and reliability. In this scenario, integrating components of the refrigeration system, with precise and synchronized control, stands out as the most prominent path toward a more sustainable and efficient future.
The fundamental question is: how can value be added to the refrigeration equipment and to the environment at the same time while ensuring better product preservation? The answer is: thinking differently about the components that are already part of the system. Currently, plug-in application manufacturers use several electronic components from different suppliers, each one with a different software, which complicates the optimization of the equipment operation. However, one can make components work in an integrated way with a common software tool for different devices, achieving performance more easily and in less adjustment time.
Key synchronized components
Component integration means that you take the key components of a refrigeration system and make them work together in a synchronized way. The key components of a usual refrigeration system are:
- Compressor: it’s the heart of the system. The most efficient are the ones with variable speed technology, featuring an inverter that adjusts the compressor’s speed to the system’s demand, resulting in significant energy savings and maintaining temperature more stable, even during peak demand.
- Fan: responsible for the air circulation in the cabinet. The versions with electronic motors have a market benchmark efficiency of up to 70%, available with single, multi, or variable speeds and different kinds of fixation methods.
- Controller: it is the electronic device that manages the system, following predefined parameters. It has the potential to enhance energy efficiency and system stability through features like adaptive defrost and adaptive door heater control.
- Development tool: Some systems could have their parameters established in a single development interface. It is what allows the synchronization of functions for optimized performance. The more “intelligent” and simplified the interface, with the possibility to automate parameters, the more it reduces the system’s setup time and simplifies the whole process.
Why to synchronize
The market shows a significant difficulty in optimizing refrigeration systems, that is, finding the balance between the ideal temperature required for food preservation and the energy consumption necessary to maintain it. Components’ synchronization greatly simplifies this task, extracting the best of each part of the system. In this sense, the energy-efficiency benefits that integrated solutions offer impact the entire industry’s value chain: from facilitating the refrigeration system’s development process to saving energy during the use phase of the refrigeration equipment. While manufacturers initially prioritize the system’s optimization, the energy savings and its resulting emissions reduction are a sustainability gain that daily becomes more urgent to the world.
So, at first, time-saving and performance improvements are the most attractive factors for adopting a solution based on components’ integration. When an engineer realizes that he can achieve optimized performance in less time, he adheres to the solution and to its positive environmental impact as well.
In our view, the integration of components is the next step in improving refrigeration equipment performance, since it delivers higher levels of energy efficiency while making the system operate synchronously and intelligently. It is the use of digitalization and electronics with a systemic view, with their maximum potential. It brings benefits such as:
- Remotely monitoring the performance of refrigeration equipment to identify usage patterns and enable adjustments to reduce energy consumption.
- Detecting problems in refrigeration equipment before they become severe. This reduces the need for corrective maintenance, avoiding the waste of resources and minimizing potential leaks of refrigerants.
- Planning preventive maintenance: With access to detailed data on equipment performance, users can implement preventive maintenance programs more effectively. This helps prolong the life of the equipment, reducing the need for frequent replacement and premature disposal of components.
- Reduction of food losses: Efficient and well-maintained refrigeration equipment helps ensure the quality and safety of stored food. This helps reduce losses in the food supply chain, contributing to more efficient use of agricultural resources and minimizing food waste.
- Rational use of raw materials: Ensuring that components are well-sized. That is an optimization of product size and, consequently, of raw material.
Better performance with sustainability
Components integration can significantly contribute to reducing carbon emissions, by enhancing energy efficiency and promoting a holistic approach to sustainability. Through the performance optimization of each component within a refrigeration system, we can maximize overall efficiency while minimizing environmental impact. This approach supports businesses by reducing operating costs and contributes to global efforts to combat climate change. As we move toward a future where everything is digitally connected, components’ integration in commercial refrigeration emerges as an indispensable path. This is the necessary step to take innovation and sustainability to the next level, using digital transformation, artificial intelligence (AI), and the Internet of Things (IoT), to achieve more performance with less carbon emissions.